Why Static Control Epoxy is Covering the Nation?
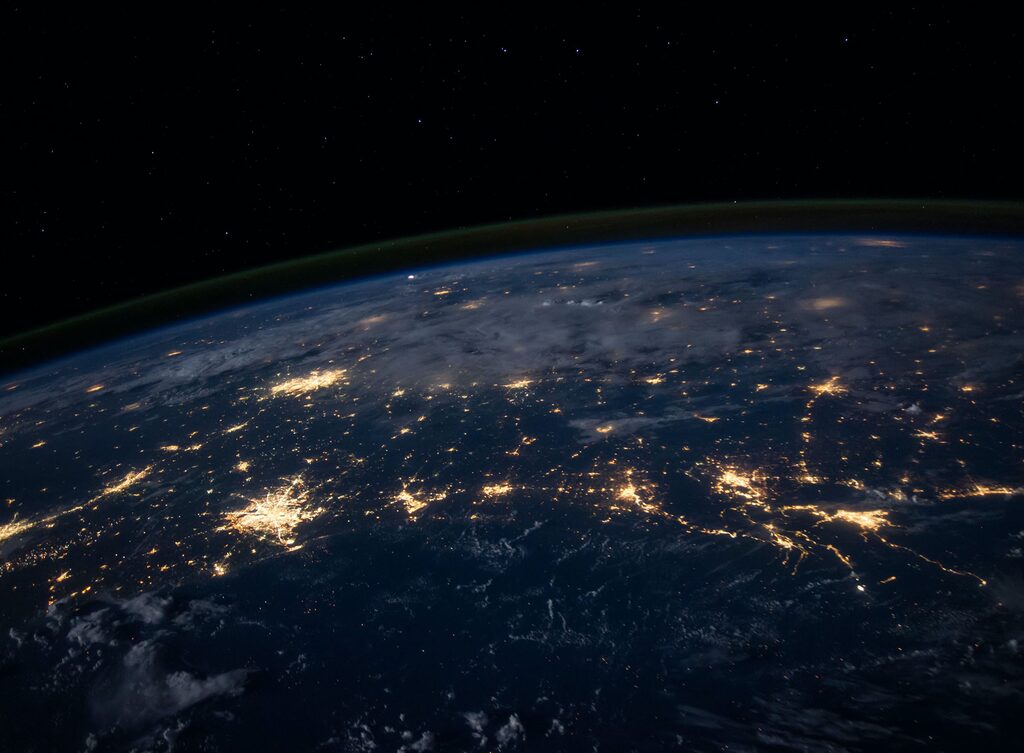
Published on:
03/03/2023
Author:
Tony Corsini
Published on:
Author:
You'll find them here.
We also post articles over all kinds of topics. Check out our posts and come back for new ones. Some things you can expect out of
THE HOOVER WELLS ADVANTAGE: